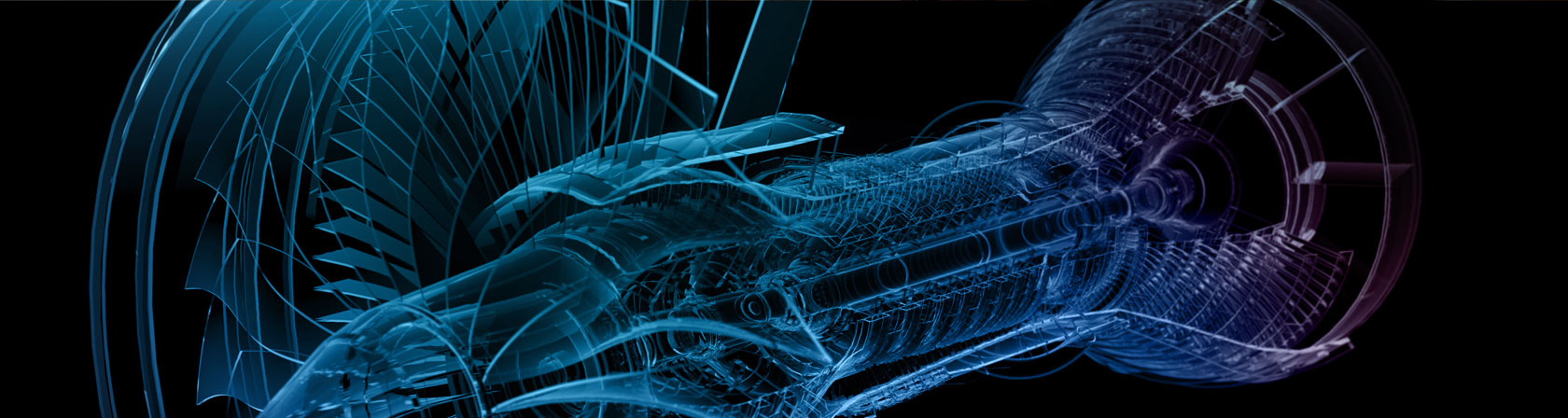
1) 5S- APPLIED 5S
2) TPM-TOTAL PRODUCTIVE MAINTENANCE;
1) Introduction to 5S
5S is traditionally looked as house keeping technique. Very few organizations like Toyota used 5S beyond just house keeping. If implemented with right spirit, 5S becomes foundation for Business Excellence Journey. Many organizations mis-interpreted 5S as just a beautification tool. They do 5S whenever customer visit is planned or during top management visits. 5S should be linked to Quality, cost and Delivery. A true 5S avoids lot of quality issues there by reduces the load on improvement projects!. Many shop-floor problems are results of poor 5S.
Over and above all this, 5S can be used to create improvement and team culture in the organization. To differentiate with traditional 5S, we renamed it as Applied 5S. Our innovation team put all the learning’s together in this program to demonstrate the power of 5S. We hope this will help you in your journey to become world-class.
2. What is applied 5S
A method of creating a lean and orderly workplace that exposes waste and in-efficiencies and makes abnormalities immediately visible;
IS Sort-(Seiri): -To remove what is not needed and keep what is needed.
2S – Set in Order/ Systematic arrangement (Seiton): Place things in such a way that they can be easily reached whenever they are needed. Keep only minimum quantity at the point of use;
3S -Shine (Seiso)- Keep things clean and polished; no trash or dirt in the workplace “don’t clean, keep it clean” “Cleaning with meaning”
4S-Standardize (Seiketsu)- Establish Standards for 1st 3S (1S,2S and 3S) Use Visual methods to expose waste and abnormalities;
5S-Sustain through Self Discipline(Shitsuke)– Sustain through continuous training & Self Discipline. Make 5S as a Culture.
3. Why Implement 5S
- It is a culture building tool;
- It is foundation for excellence;
- It is simple but powerful and everyone can understand easily;
- It can be applied to all Industries and Institutes;
- It can be applied at home;
- Children can apply it at schools.
4.What benefits 5S can and brought to business:
- 10,000 sq feet of space released after effective 1S activity, which was converted into a training center – Mfg industry;
- Any Document/tool retrievals in less than 30 seconds by anyone – Service Industry;
- Equipment Breakdowns reduced by 50 % due to effective cleaning and maintenance by the employees;
- Employee discipline/punctuality improved;
- Productivity improved by 15 % after implementation of 5S pledge in a garment Industry;
- Quality issues due to mix-up, confusions, wrong identification are completely eliminated;
- Auditors – Customers, potential customers impressed with the workplace enabling organization for new business;
- Employee engagement improved significantly and helped in cultural transformation
5. Applicable to:
It can be applied in Warehouse, construction, retail, pharmaceuticals, chemical, paper and pulp, glass, ceramic, steel, cement, Schools, colleges, hospitals, diagnostic centers, libraries and IT companies;
6.Approach:
- Formation of Core team and defining roles and responsibilities;
- Zone formation in Shop floor and identifying Zone leaders;
- Training Core team members on 5S;
- Training 100 % employees on 5S by core team using local language;
- 1S and 3S workshop;
- Clearing of all RED tag items;
- Development of 5S Standards Manual;
- 2S and Visual Management Implementation-Model Zones;
- Horizontal deployment of 2S and Visual Management in all zones;
- Disposal of all items on using RED tag method and necessary approvals;
- 5S Auditor selection and Training;
- First Audit of 5S in all zones by core team;
- Initiate formal Audits (every month);
- Introduce Rewards and Recognitions;
- Continual improvements through Kaizens, Visuals ,Kanbans etc.,
1.Introduction to TPM (Total Productive Maintenance)
TPM is a maintenance philosophy aimed at eliminating production losses due to equipment status, or in other words, keeping equipment in a position to produce at maximum capacity, the expected quality products, with no unscheduled stops. This includes:
- Zero breakdowns
- Zero downtimes
- Zero failures attributed to poor condition of equipment
- No loss of efficiency or production capacity due to this equipment
It is understood perfectly the name: total productive maintenance, or maintenance that provides maximum or total productivity.
2.What is TPM (Total Productive Maintenance)
It can be considered as the medical science of machines. Total Productive Maintenance (TPM) is a maintenance program which involves a newly defined concept for maintaining plants and equipment. The goal of the TPM program is to markedly increase production while, at the same time, increasing employee morale and job satisfaction.
TPM brings maintenance into focus as a necessary and vitally important part of the business. It is no longer regarded as a non-profit activity. Down time for maintenance is scheduled as a part of the manufacturing day and, in some cases, as an integral part of the manufacturing process. The goal is to hold emergency and unscheduled maintenance to a minimum.
3.Why TPM (Total Productive Maintenance)
- Avoid wastage in a quickly changing economic environment;
- Producing goods without reducing product quality;
- Reduce cost;
- Produce a low batch quantity at the earliest possible time;
- Goods send to the customers must be non-defective.
4.What benefits it (Total Productive Maintenance) brings to Business:
- Productivity improvement;
- Machine utilization;
- Defects reduction;
- Reducing unexpected breakdowns;
- Reduce accidents;
- Reduce consumable and spares cost.
5.Applicable to:
Applied to all types of industries including Engineering, Service, Information Technology, Construction, Real Estates, Apparel, Healthcare, Hospitality, Education, Pharma and Process Industries.
6.Approach:
- Preparing cation plan for TPM implementation;
- Identify an area for a pilot TPM program;
- Focus on restoring targeted equipment to prime working condition;
- Begin to measure Overall Equipment Effectiveness (OEE);
- Address Major Loss Causes;
- Implement proactive maintenance;
- Implement specific TPM concepts as needed.